Experimental and Numerical Analysis of the Clinching Process with Segmented Die in Comparison to Alternative Joining Methods
DOI:
https://doi.org/10.37934/aram.137.1.134146Keywords:
clinching, simulation, LS-DYNA, mechanical joining, finite elementAbstract
Clinching is an advanced cold joining method for sheet metals that eliminates the need for additional materials to assemble parts. It involves the plastic deformation of metal sheets to create a joint. The process relies on the interaction between a punch and a die, without the use of any coatings or additives. The punch applies a predetermined force, causing the metal sheets to be pressed through the die cavity and filling the groove, resulting in an interlock point. The final shape of the clinched joint is determined by the tool's geometry. In this study, we investigated the clinching process using segmented die and finite element (FE) methods. The numerical analysis was conducted using LS-DYNA software on AA5052 aluminium and mild steel sheets. Additionally, we compared the compression between spot welding and clinching. The results of our study revealed that various process parameters significantly influence the clinching process, including the bottom thickness, neck thickness and interlock length. Among these factors, die height emerged as the primary influencing factor. Furthermore, we found that the energy absorption and stiffness of the clinched joints were lower compared to those of spot welding.
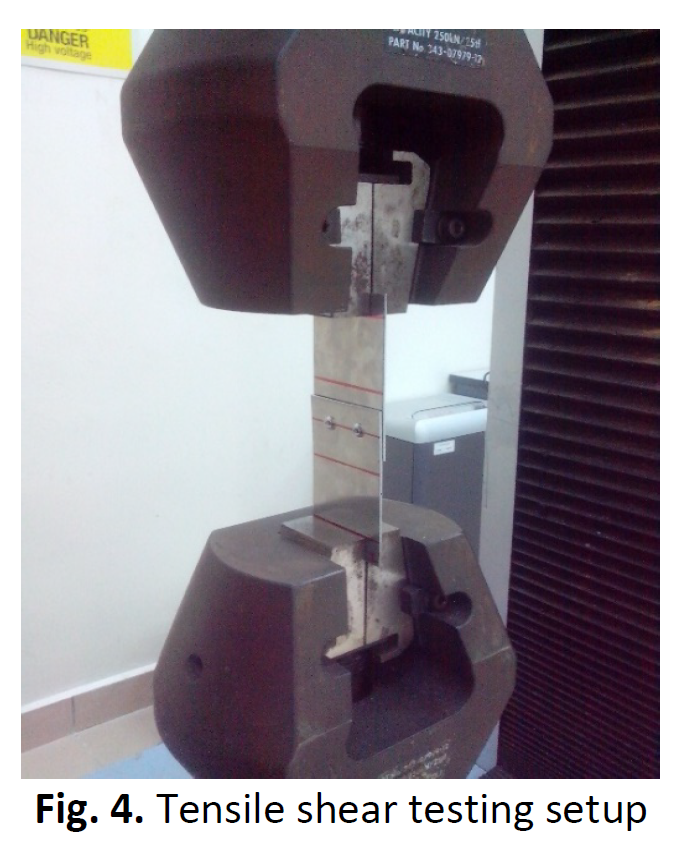