Tool Deterioration of AISI 4340 Steel Machining under Minimum Quantity Lubrication (MQL)
DOI:
https://doi.org/10.37934/aram.137.1.2135Keywords:
MQL, Taguchi L9 method (34), DCMT11 insert tool, tool deterioration, coolantAbstract
Lubrication is crucial in mitigating the wear and tear experienced by AISI 4340 steel during machining processes. Traditional lubrication methods have excellent cooling capabilities; this condition leads to losses in several aspects, one of which is tool damage. Whereas the Minimum Quantity Lubrication (MQL) technique proves effective by blending controlled amounts of lubricant with air pressure, targeting the workpiece. This research focuses on evaluating tool performance within the MQL framework during machining operations. The MQL system's parameters, such as time and temperature, were observed using an Arduino-controlled setup. The Taguchi orthogonal array L9 (34) methodology was applied to design and analyse experiments. Four variables, each with three levels, were considered: cutting depth, cutting speed, coolant application method and feed rate. The assessment of tool deterioration encompassed five damage levels: (1) scratching, (2) tool delamination, (3) burning, (4) built-up edge (BUE) and (5) chipping. Evaluation extended to three viewpoints: flank, left and right sides. The outcome revealed that cutting speed was the predominant factor influencing tool deterioration at 49.81%. The method of coolant application, feed rate and cutting depth accounted for 35.81%, 16.15% and 11.79% of the impact, respectively. Optimal results, indicating minimal tool deterioration, were achieved with the following parameter combination: cutting depth of 1.8 mm, cutting speed of 120.89 m/min, periodic MQL application and a feed rate of 0.107 m/rev.
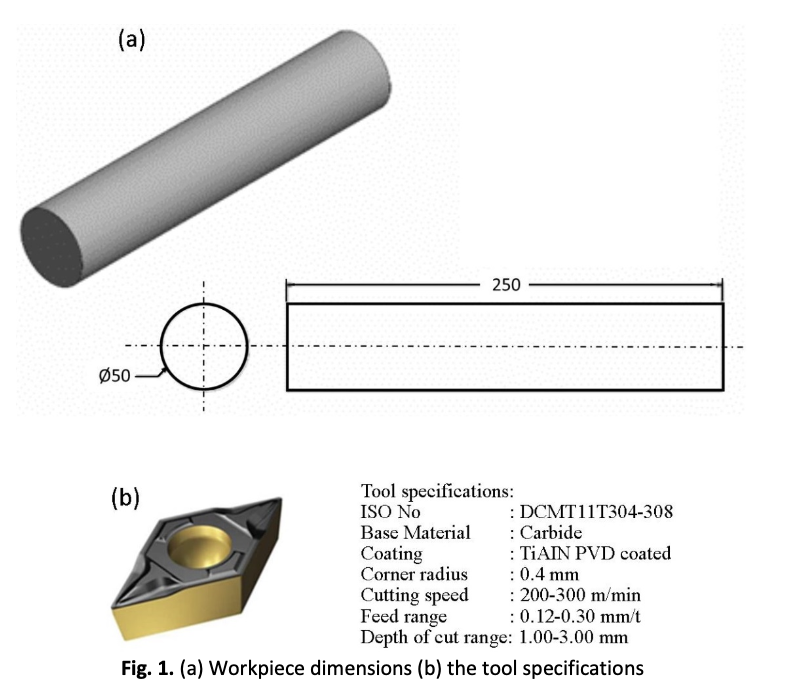