Mechanical Properties of Composite from Roving Fibre and Polyester Resin BQTN R157 Variations Manufactured using Vacuum Bagging Method for Unmanned Aerial Vehicle Applications
DOI:
https://doi.org/10.37934/aram.137.1.5866Keywords:
Composite, fiber, mechanical properties, reinforced, tensileAbstract
A study on the mechanical properties of roving fibre-reinforced polyester resin composites was conducted, focusing on tensile tests with fibre orientations of 0°, 90° and 45°. The composite was fabricated with a fibre-to-resin mass fraction of 60%:40%. The objective of this research was to analyse the micro and macro properties of roving fibre composites with polyester resin for unmanned aerial vehicle (UAV) applications. Micro properties were evaluated through density testing, while macro properties were determined via tensile strength testing following ASTM D3039 standards. The UAV application was further analysed against the atmospheric pressure and altitude requirements based on the International Standard Atmosphere. Composite fabrication employed the vacuum bagging method with a consistent 60% fibre and 40% resin volume fraction. Results indicated that the highest density, 1.844 g/cm³, was achieved with a 45° fibre orientation. The study revealed that increased fibre content corresponds to higher composite density. Tensile tests demonstrated that the highest tensile modulus of 25,255.33 MPa, was obtained with a 90° fibre orientation. Atmospheric pressure analysis for UAVs showed that the 90° fibre-oriented composite exhibited superior strength compared to air pressure, achieving a maximum stress of 641.96 MPa. These findings confirm that the composite with a 90° fibre orientation meets the required air pressure standards for UAV construction, demonstrating high suitability for such applications.
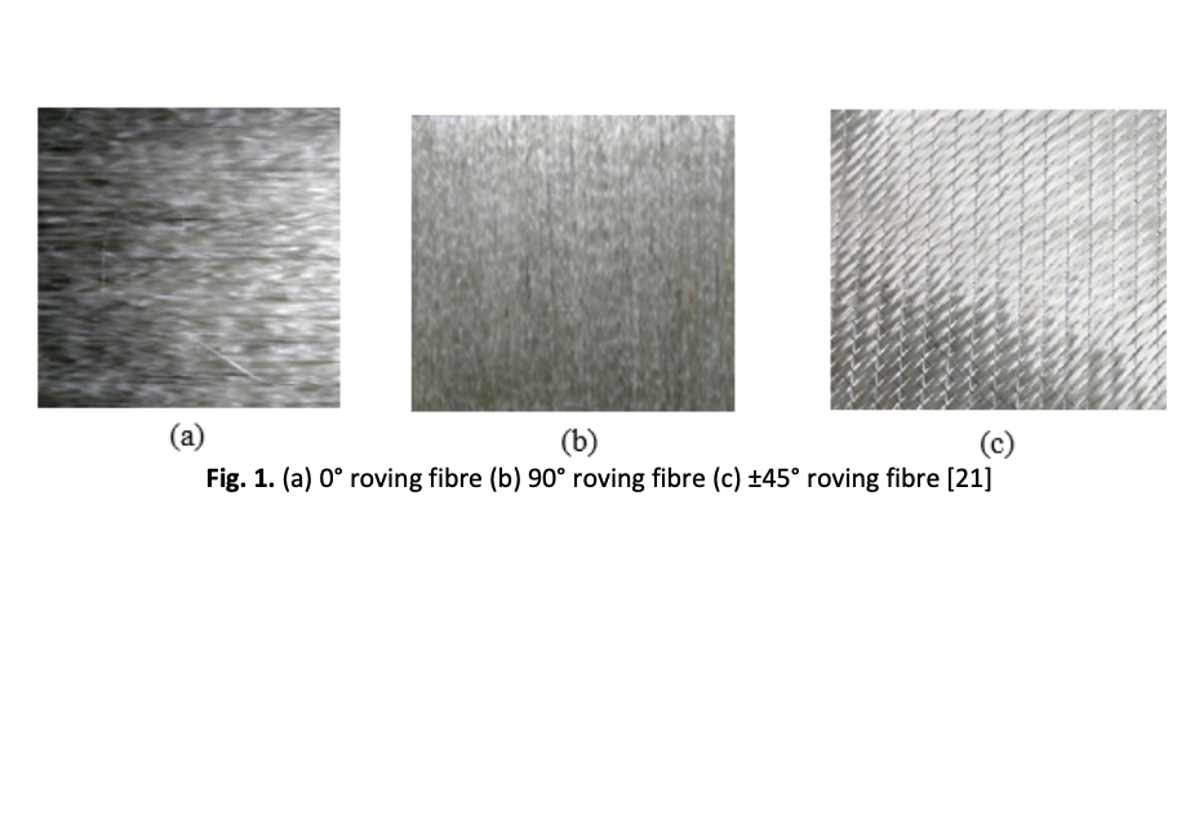